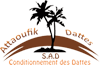
Our vocation is to bring complete satisfaction to our customers, relying on the quality of our products and the commitment of our teams. We are committed to providing products that meet customer demand for food safety. The management gives priority to the management system of quality, food safety, environment and good agricultural practices in accordance with the requirements of ISO 9001, ISO 22000 as well as the HACCP principles and methods. Many years of experience make it possible to refine the selection criteria in order to only supply products that comply with the product quality charter. In line with our objectives, the General Management is committed to implementing all the necessary means that will enable us to provide services that meet customers’ demands in terms of food safety, time, cost, quality of implementation and protection of the environment. It is also committed to constantly improve the quality of the company’s services, while ensuring its sustainability.
With the slogan “Quality, Authenticity, Safety”, Attaoufik des Dattes has the mission to ensure the quality of service throughout the year and guarantee consumers the quality, authenticity and food safety of our dates while minimizing environmental impacts. Our quality policy focuses on the following points:
The satisfaction of our customers comes always first. We listen carefully to our customers and take their feedback and remarks into account in order to provide them with the best products and services according to their requirements. We ensure the quality, traceability and food safety of our products beyond the requirements of the market. Our goal is to be perceived by our customers as a partner that helps them achieve their goals.
Our quality system is designed and implemented to enable our organization to meet the expectations of our customers:
We strive to constantly improve our services, in order to maximize the economic performance of the company, by pooling synergies, optimizing our processes and work procedures, adopting a common approach to improve the quality of our products, rationalizing production costs and implementing the necessary means to ensure the safety and health of employees at the workplace.
We want to develop the knowledge and skills of our employees according to specific objectives. They are the promoters of our services and our innovations. Through transparent and direct communication, we aim at creating a climate of motivation, creativity and trust that will allow us to achieve the desired successes together.
Every employee and every producer contributes to ensuring the quality and the food safety of the products by the quality of his work. Quality is the responsibility of everyone. In accordance with the requirements to be met, we rely on producers and staff whose attitude is positive towards food safety and quality as well as the environment and the organization.
Our commitment to the values of Quality, Safety and Environment are always accompanied by a desire to move forward. It is innovation that will boost our Quality, Safety and Environment system. The driving force behind our ambition is to always better satisfy our customers by anticipating their needs. To achieve this, our Quality, Safety and Environment policy must be understood, shared and accepted by all. In this way, we will be able to identify and then permanently eliminate our dysfunction and to make our customers, partners, employees and shareholders benefit from the progress made.
A quality, safety and environmental approach is first and foremost an improvement process.
We select efficient and innovative suppliers who are committed to the same principles of quality as our own. Verification and control can be done through audits at our suppliers as well as through a control system at the reception of the products.
Our partners and suppliers are also concerned by our quality process and agree to undergo regular strict controls to maintain an optimum level of quality of their products.
The continuous improvement of a quality management system consists of increasing internal performance and customer satisfaction. This includes, among other things:
– analysis of results to identify areas for improvement and goal setting.
– research and implementation of improvement actions and evaluation of results.
– formalization of changes.